Inventory refers to all the items/raw materials held by a business used to produce finished goods or for selling in the market to earn profit. You can easily keep track of stock items using the inventory management tools in Dynamics365 NAV. First, you need to set up locations in a warehouse with their details.
Item Setup: To set up items that are currently available in stock, specify their unit of measure, costing method, inventory posting group, unit cost and price and other properties. There are three types of items as follows:
- Inventory: Items that are needed for day-to-day production/selling and has high value.
- Non-Inventory: Low-cost physical Items for internal use that are not a part of regular inventory but are ordered as per requirement.
- Service: Non-physical Items which represents services/Labour time.
Warehouse Setup: Each user performing warehouse related activities must be set up as a warehouse employee assigned to a particular location.
Bins: Items can be assigned to bins for better management of inventory. In location master, if you have checked the Boolean – “Bin mandatory”, then you need to specify bin whenever you try to move the stock within the warehouse.
Item Tracking: Serial No. and Lot No. are tracked by Item Tracking. You can manage stock using serial numbers or Lot numbers. Assigning these numbers can be manual or automatic as per the requirement of the user.
Stock Transfer: Stock can be moved from one location to another by creating transfer orders. Using this, you ship the outbound transfer from one location and receive inbound transfer at the other location. You can also use an item reclassification journal to transfer stocks.
Picks and Put Aways: Create pick and put-away orders. If you want to make Pick/Put-Away mandatory, then you need to tick the check box “Require Pick”,” Require Put-Away” available in Location Master.
Warehouse Receipt: In the purchase order, you can find the action named Created Warehouse Receipt. By clicking this, the warehouse will be expecting the goods as on the delivery date. Once received, the goods are moved to their assigned bin in a storage location.
Gate Entry: Gate Entry is the record of goods entering/leaving the premises. This also helps in tracking the vehicle details, time in and time out, the person accompanying the vehicle etc.
Physical Inventory Counting: This process is done periodically to verify whether the total physical count of the inventory matches the NAV inventory count. If the values are mismatched, then the difference is posted via positive/negative adjustment in the physical inventory journal. Item transactions, such as sales, purchase, negative and positive adjustments can be posted from item journals.
THE FOLLOWING IMAGE EXPLAINS THE WAREHOUSE FLOWS
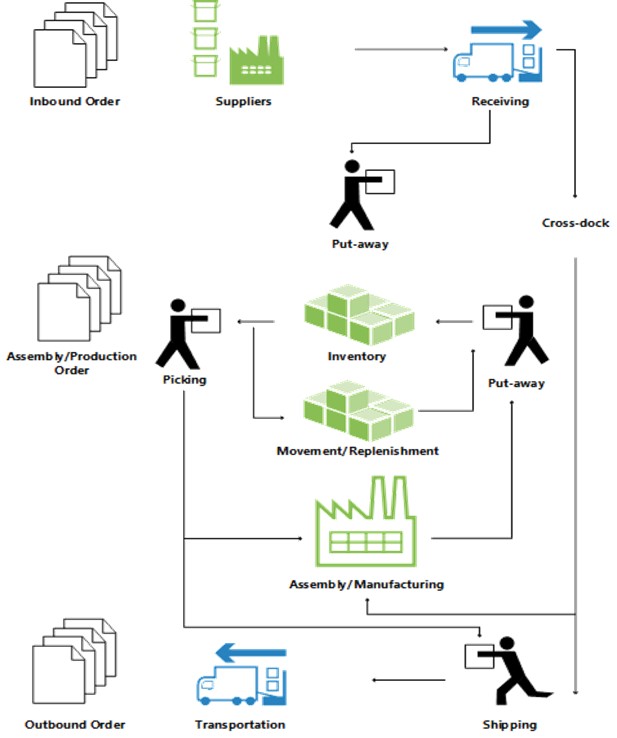