ERP Solution for the Chemical Industry
Our solution for the chemical industry is one of the preferred ERP applications when it comes to managing the various complicated operations involved in a chemical manufacturing/processing business. Our Enterprise Management clearly stands out when it comes to adapting to the diverse needs of the chemical industry.
Diverse features of our Chemical ERP software let you perform and manage critical activities like processing raw materials, scheduling tasks, importing and exporting, quality analysis, etc. in an easy and efficient way. India is the fourth-largest producer of agrochemicals in the world, hence, the agrochemical-based industries in India shoulder a huge responsibility of supply. Our ERP software solutions come with these powerful features to make things smooth and easy.
Chemical Solution Functional Coverage
-
- Complex & Multi-Level Formula & Recipe Tracking
- Data and Business Intelligence Sharing
- Certificate of Analysis Creation and Reporting Compliance
- Comprehensive Quality Parameters Management
- Inventory Management with Make to OrderStock Scenario
- Yield and Waste Management
- Batch Scheduling and Planning as per Packing Sizes
- Accurate Product Costing
- Financial Management with Costing and Budgeting
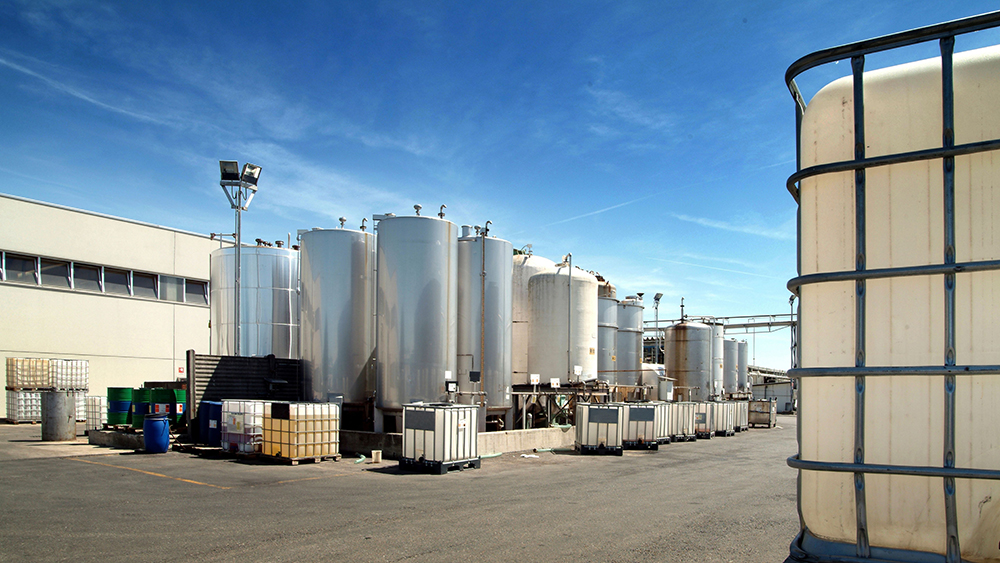
ERP Features for Chemical Industry
-
- Formula security to support Intellectual Property Rights (IPRs)
- Supports OSHA, EPA, ISO, DOT compliance requirements
- Supports GHS Labelling requirements
- HAZMAT bills of lading, VOC, and SARA reporting
- Bi-directional lot traceability
- Vendor approval and management
- Stability testing
- Non-Conformance and CAPA
- Complete traceability and costing of by and co-products
- Customizable COA (Certificate of Analysis) reports
- Formula design based on physical properties
- Separate costing of formula and packaging materials
- New product development and its costing
- Warehouse management
- Shelf life / Expiration date support
- Supports multiple units of measure
- Containerization
- Make-To-Stock and Make-To-Order Operations
- Material Production Scheduling (MPS)
- Material Requirement Planning (MRP)
-
Chemical Industry-Specific Reports
- Yield Analysis Report for tracking spillage or losses
- Certificate of Analysis (CoA) Reports
- Product-wise Ageing and Expiry Tracking
- Traceability Reports from RM receipt to Dispatch
- Pre-Process, In-Process, Post Process, and Inventory QC Reports
- Customer and Vendor Ageing Reports
-
Why ERP for the Chemical Industry?
- Quality Assurance
- Compliance and Regulation
- Safety Management
- Inventory Tracking and Planning
- Accurate Reports
- Finance Management
- Quality Control
- Stock Handling
- Expense Management
- Resources Management
- Production Management